Colour measurement of granulate, a good idea?
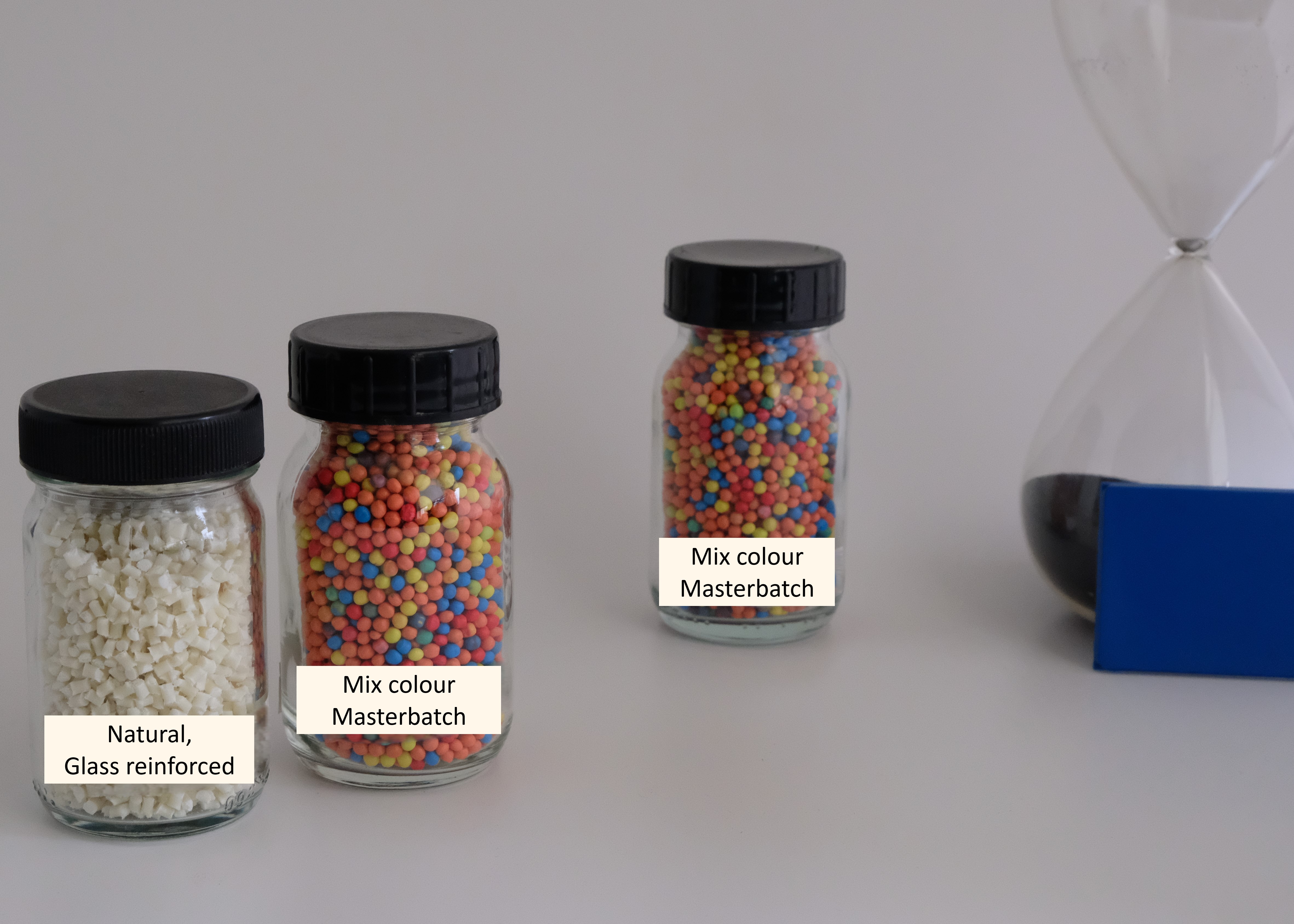
Is measuring colour of granulate Engineering Plastics a good idea?
Short answer: YES!.... Longer answer: Well, not in all cases!
A laboratory is all about quality, in the broadest sense of the word. Subsequently, efficiency increases are continuously examined: what is relevant to do or not to do and in what way.
For Engineering Plastics the colour is determined on an injection moulded plate of about 3 mm thick; there are materials, such as Polycarbonate, where you can also determine the colour on a pressed plate (pancake), but a large number of polymers, such as Polyamides, then discolour under the influence of oxygen and elevated temperature.
Such an analysis (of injection molding, cooling and colour measurement) can easily take an hour and time is essential for a production process, where about 2-8 tons of plastic is produced per hour.
So you are regularly asked, after each Management change, whether you can also determine the colour, for SPC purposes, on the granules or granulate.
But that's not so easy, because you have to deal with variation in the composition, where at one time the granulate is smooth and regular in shape, but at other times contain glass and are very rough and irregularly chopped; in addition, you also have to deal with variation in the production process and thus also the chopper or underwater granulator.....not to mention the blind spots of those granules in a cuvette with which you determine the colour; all those granulate just not aligning or overlapping each other, causing a lot of blind spots and a totally non-homogeneously smooth measuring surface.
All this leads to enormous variations in colour results and given the extremely narrow colour specifications of coloured Engineering Plastics, granulate measurement is not an alternative for colour measurement on injection moulded plates.
Is colour measurement so much better after injection molding? Yes, there is an extra heat treatment...but the customer also has that when making the final product, so a better correlation. Yes, colour measurement of injection moulded plates also has its variation and often the specifications are defined so narrowly (and sometimes not fitting the material) that the Gage %R*R is above 30%..... I will write a separate blog about this topic sometime!
But the variation in colour measurement of granulate is still a factor 2-3 higher.
Is the granulate measurement relevant at all? Yes... it is an excellent tool for naturals, for example, where the colour should only be indicative and directional, if the question is whether the polymerisation or compounding went well and whether or not too much degradation or oxidation occurred. And if your granulate shape is regular and stable and the colour specification is not that narrow, then a granulate measurement is a good alternative.
Are there no time-saving alternatives for narrowly specified coloured materials? Yes, there are, but not yet widely applicable. A very interesting development in recent years is the in-line measurement in the molten plastic (head of the extruder for example), whereby the probe sensors are more and more resistant to the high temperatures and pressure during compounding. This technique is promising in order to work more efficiently while maintaining quality; and since you can measure continuously, you are better able to monitor and optimise the colour quality of the entire batch and process. Companies such as Colvistec and Elsolab are suitable candidates to spar with.
Ergo: Choose granulate measurements for indicative good/false assessment of the colour and with broader colour specifications; with narrowly specified plastics, the colour analysis of an injection moulded plate is still the most accurate and representative.
If you would like to know more or exchange ideas about the possibilities at your location, please contact weColLaborate: www.wecollaborate.nl/en
Feel free to contact us or request a quotation