Injection Moulding coloured Engineering Plastics?
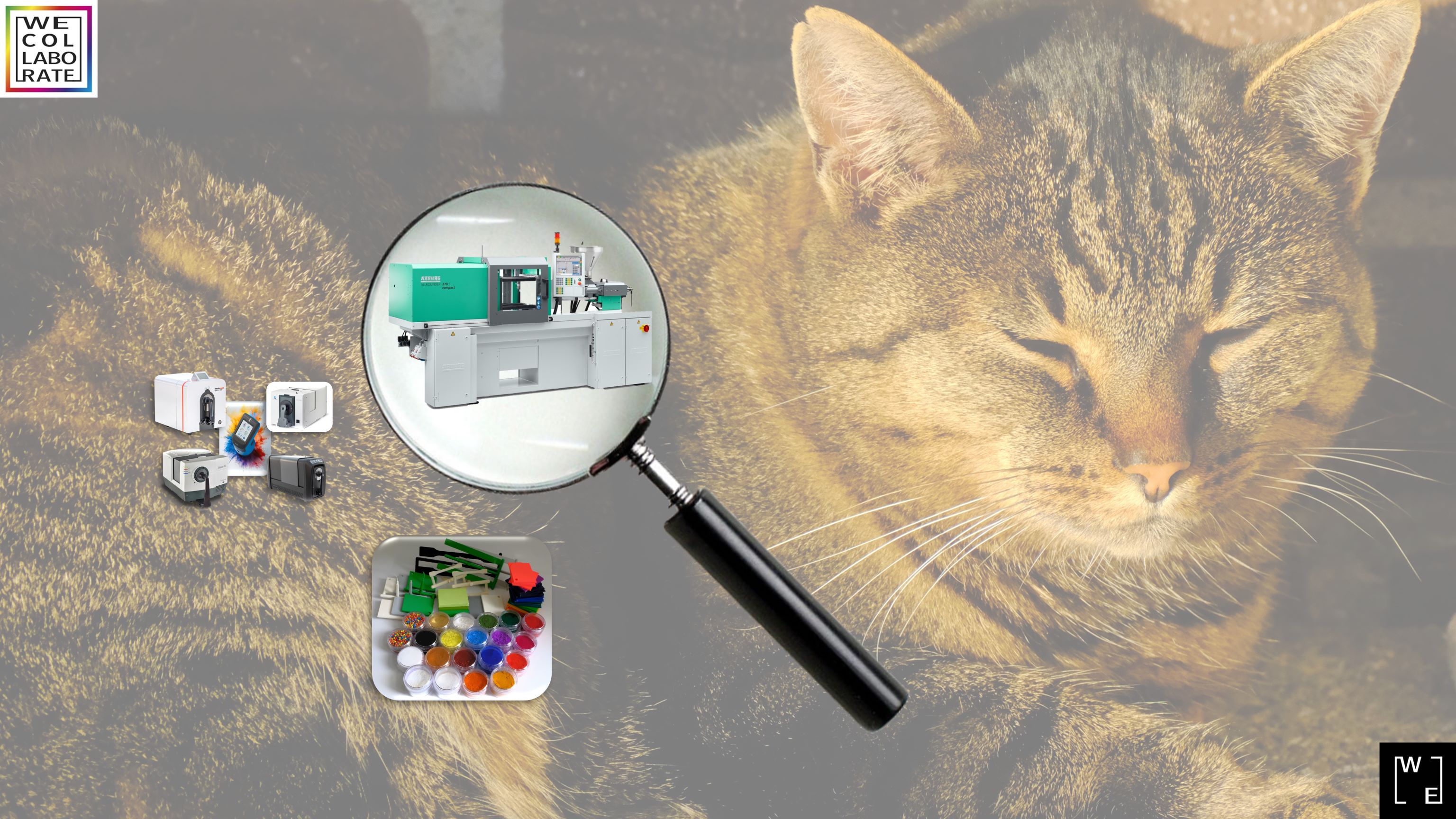
Injection moulding is still the most commonly used technique for plastic (semi-finished) products, especially when producing larger series quickly and efficiently. And to analyse the quality of the produced plastics granulate, standardised injection-moulded bars and plaques are used.
The choice of a particular plastic naturally depends on its properties in relation to the application: Is a dimensionally stable and high-temperature-resistant plastic required? Is an impact-resistant material needed that does not deform, or deforms as little as possible, even at higher temperatures? Is a flame-retardant or flame-extinguishing plastic required? Is RAL 2003 orange colour the prerequisite for the application? Is a material needed that can be laser marked?
The application and the subsequent necessary properties of the plastic also determine which analyses must be carried out. All these analyses are set in ISO standards and the (local) work regulations are usually derived from them; in daily business it is necessary to draw up more specific and workable (simpler) instructions. And not only the injection moulding itself, but also the preparation (moisture, representative sampling) and the conditioning after injection moulding and prior to the analysis are described.
What applies to every profession and craft certainly also applies to the analysis of plastics, namely that well-trained laboratory technicians carry out the analyses. The very good “Injection Moulding” education (in the Netherlands “NRK”, translated: Rubber and Plastics Industry, confederation recognised diploma) cover various aspects, from polymer types to screws, from speeds and pressures to temperatures, from homogeneity to moulds.
The emphasis in these training courses is on safe operation of the machine and optimal quality of the injection moulded objects. For the analysis, these objects include bars for tensile strength, Charpy, UL and plaques for glowwire, hardness and also colour.
What’s been given less attention is what needs to be done after injection moulding, what is required to perform a good and correct analysis, and what happens to the polymer after injection moulding.
A plastic is pushed fairly quickly through a small hole at a high temperature and the necessary pressure and cooled considerably in the mould. The polymer chains, amongst others, are pressed in a certain flow direction and it takes “a while” before these chains relax to their own, polymer-specific, orientation. This is different for each type of polymer and plastic and can sometimes take several days.
It is because of this aspect that the conditioning prior to the analysis of the material properties (and, I assume, also the assembly of semi-finished products!) takes at least 24 hours.
The analyses of material properties are not steering parameters during the compounding of plastics; viscosity, composition and moisture are indicators (secondary properties) that production has gone well and afterwards, tensile strength, Charpy and UL, among other things, are analysed for the final determination of quality and for the release of a batch.
But what does this mean for colour?
Colour is most certainly a steering parameter and everything is aimed at analysing this as quickly as possible. You don't want to find after 24 hours that your batch of 50 tons (or more) is outside the colour specification; the majority of colour analyses must be completed within an hour and after injection moulding, cooling of the colour plaque is usually for a maximum of 15 minutes before measuring the colour.
But is this correct? How much does the colour change after injection moulding during the relaxation time? Is this ever checked or investigated?
We know a lot about crystallisation and what factors contribute to it, but do we also know this for all pigments (inorganic and organic) and dyes, let alone their combinations? Inorganic pigments do not dissolve in the polymer matrix and at most contribute to the crystallisation rate, but is this reproducible? Dyes can have more difficulty spreading in the crystalline part and a few dyes even slow down the crystallisation rate, what does that do to the colour? In my experience I can name at least a few organic pigments and dyes that require longer than the 15 minutes cooling time after injection moulding to develop the final colour.
The analysis instructions are now “one-size-fits-all”, regardless of the analysis, and during injection moulding the inserts in a mould are changed for the different bars and plaques; that is of course very efficient. But is this the right way or approach? Instead of injection moulding as efficiently and quickly as possible, should you perhaps switch to the total analysis time to be as efficiently and quickly as possible? Can you adjust the injection moulding settings in such a way that the relaxation time after injection moulding is minimised, so that you either save time in conditioning or can analyse the colour (and perhaps other properties) faster and more correctly?
It might be time to take a closer look at this hundred-plus old technique, time to relax!
Feel free to contact us or request a quotation