L*a*b* are KOPs!
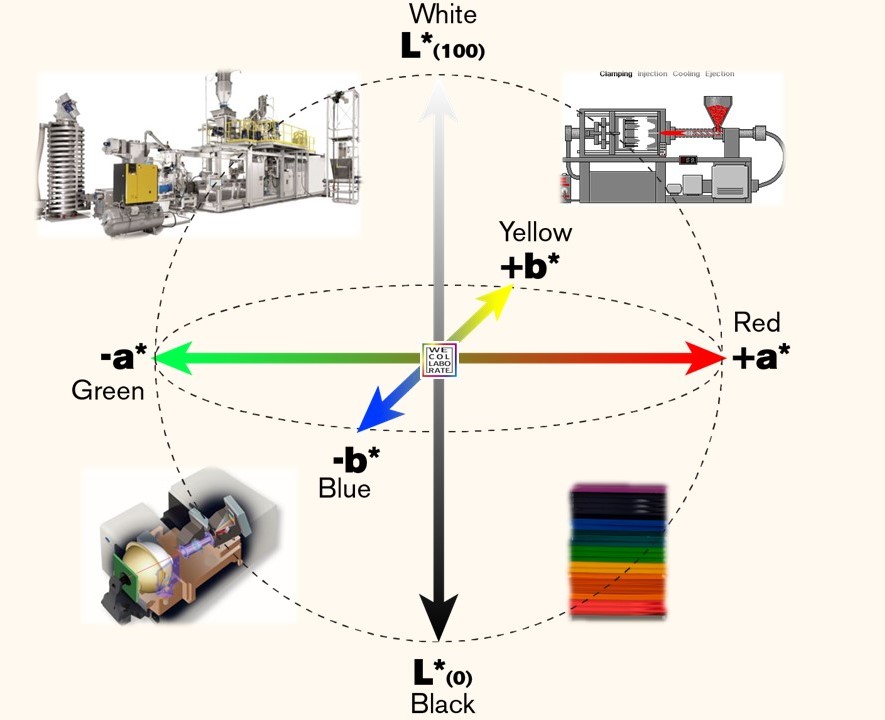
If you talk of compounding (or extrusion) of plastics, then you’re talking about raw materials, feeders, screws, chopper and vibrating coolers.
When determining the quality of the Engineering Plastics produced, you’re talking about composition (glass or mineral content), moisture, mechanical properties and also colour.
For the quality of the extrusion process itself, you consider the "Key Operating Parameters" (KOPs), meaning the most important process parameters, such as speed, yield, temperature (zones, head, melt, vacuum) and pressure (vacuum, head), torque, specific energy...
But seldom is colour mentioned in this!
And that is a bit strange, because colour is the only (and most visible) parameter that does not have a sufficient link with the existing KOPs: When the gravimetric feeder is set precisely, you will measure the correct glass content in the analysis afterwards; if the screw geometry is accurate and the temperatures are set correctly, you will produce a good homogeneous plastic compound that has the right viscosity and mechanical properties in the analysis afterwards.
But colour can differ, even if you have set everything correctly: pigments and dyes vary, not to mention masterbatches and colour concentrates, and have an influence on the colour of the plastic compounds. And this is all about significance!
Nonsignificant deviations in vacuum or raw material content (variation, segregation) can have a significant influence on the colour, interactions between the raw materials or the same raw material from another supplier rarely have a significant influence on mechanical properties, but can have a huge influence on the colour. Colour is the sum of all (small) variations in process and raw materials.
And of all the material properties, the L*a*b*'s are often the parameters with the very narrow specifications.
And yes, there are different start-up and control protocols, to at least get a good start, but what happens in the course of production (which can take hours)....a colour analysis can easily take half an hour, you can't measure every granule and you don't want to have to homogenise every batch. Minimum productions are easily 50-100 tons of Engineering Plastics!
It surprises me sometimes to see how coloured plastics are produced - how people find it difficult in production - how so much can still be optimised with sometimes minimal adjustments - the lack of knowledge and skills about what the colour, and variation, signify, not only for coloured, but also natural plastics - how you deal with specifications of both the plastics and the raw materials and what requirements you demand from suppliers.
Not even mentioning the process of colour development, where the foundation is laid for repeatable, reproducible and labour-efficient colour productions.
Colour analysis by Engineering Plastics is still most reliable when done on (good and correct) injection moulded plates; no other technique is (yet) available that can do this with comparable quality, especially not in relation to the often very narrow specifications (although there is still something to be said about the relevance and feasibility).
For the determination of the final colour it may therefore remain the method of choice, if only because customers also determine the colour on the basis of injection moulded applications.
However, for the continuous monitoring of colour, there are now a number of potentially good sensors and/or devices on the market that are worth investigating, such as the “Hyperspectral Imaging” camera from Konica Minolta or the “Inline Spectroscopy” system from Colvistec (not just colour!).
Furthermore, I've said it before (see one of my previous blogs!), the analysis of coloured plastics granulate in a cuvette with a spectrophotometer is not the solution!
Colour is the most visible material property and not only a measure of the quality of the coloured applications, but also a measure of the reliability of the compounding process of both coloured and natural plastics. None of the other material properties give such a direct signal that something is deviating and colour can be a valuable parameter for adjusting and optimising your process. And if you know how to interpret colour values, it also indicates the direction of the root cause of the variation or deviation.
It's time for the colour parameters to be recognised and introduced as a KOP!
If you want to optimise your compounding and/or injection moulding process, please contact weColLaborate for evaluation and advice.
Feel free to contact us or request a quotation